What is an AC contractor?
In the huge system of industrial electricity, the AC contactor is like a silent but crucial behind-the-scenes hero. An AC contactor is an alternating current contactor, an automatic electrical device that uses electromagnetic principles to control the on and off of a circuit. Its English name is “AC Contactor”. The core principle of its work is based on the law of electromagnetic induction. When the electromagnetic coil of the contactor is energized, the current passes through the coil to generate a magnetic field. This magnetic field is like an invisible but powerful hand, which makes the static iron core generate electromagnetic attraction and attract the moving iron core to move. As the moving iron core moves, the contacts connected to it are also closed or disconnected accordingly, thereby realizing the on and off control of the current in the main circuit. This process is like a traffic light that directs traffic, and through orderly “opening” and “closing”, it ensures the normal operation of the circuit system.
From its appearance, the AC contactor usually has a sturdy shell, and the electromagnetic system, contact system, arc extinguishing device, and other key components are integrated inside. The electromagnetic system is its “brain”, responsible for receiving and processing control signals and issuing action instructions; the contact system is like the “throat” of the circuit, directly controlling the on and off of the current; and the arc extinguishing device is like the “firefighter” of the circuit, quickly extinguishing the arc when the contact is disconnected, avoiding damage to the equipment caused by the arc, and ensuring the safe and stable operation of the circuit.
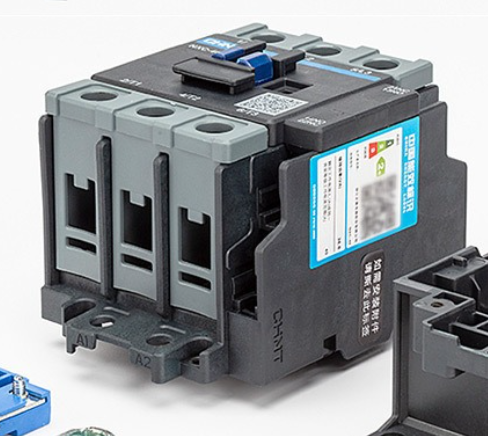
Why is it so important?
AC contactors occupy a pivotal position in the industrial field and can be called the “nerve center” of industrial equipment, playing an indispensable and key role in many aspects.
- Frequent start and stop control: On the production lines of various factories, motors are the power source for driving various mechanical equipment, and AC contactors are responsible for frequently controlling the start and stop of motors. Taking automobile manufacturing plants as an example, the motors of mechanical arms, conveyor belts, and other equipment on the production line need to be frequently started and stopped according to the requirements of the production process. AC contactors can respond to control signals quickly and accurately, realize frequent start and stop operations of motors, and ensure efficient and orderly operation of production lines. According to statistics, in some factories with a high degree of automation, an ACcontractor may perform hundreds or even thousands of start and stop operations every day. The stability and reliability of its work directly affect the continuity and production efficiency of the entire production process.
- Remote control function: With the development of industrial automation and intelligence, remote control has become an important demand for modern industrial production. The combination of AC contactors and control systems can easily realize remote operation, allowing operators to remotely control the equipment through computers or other intelligent terminals away from the control center of the equipment. In large power substations, workers can control the on and off of power equipment by operating AC contactors in the monitoring room through remote control systems, realizing remote management and monitoring of power distribution. This remote control function not only improves work efficiency but also reduces the risk of personnel working in dangerous environments, providing a strong guarantee for the safety and convenience of industrial production.
- Overload protection function: In industrial production, due to various reasons, the equipment may be overloaded, which will cause serious damage to the equipment and even cause safety accidents. The AC contactor is equipped with an overload protection device. When the current in the circuit exceeds the rated value, the overload protection device will automatically operate to cut off the circuit and protect the equipment from damage by overload current. For example, in mining, the motors of large mining equipment are prone to overload when encountering ore blockage and other situations. At this time, the overload protection function of the AC contactor will come into play, cutting off the power supply in time to prevent the motor from burning due to overload and,at the same time, ensuring the safety of the entire mining operation.

Troubleshooting guide for learning in one go
Although AC contactors are key players in industrial production, they are also inevitably “sick” and have various faults. Once a fault occurs, if it cannot be checked and solved in time, it is very likely to cause production stagnation and serious economic losses. Next, let’s explore the troubleshooting and solutions of common faults of AC contactors.
Contact ablation: the fatal injury of poor contact
During the operation of AC contactors, contact ablation is a common and more harmful fault phenomenon. When you turn on the contactor, if you find that the surface of the contact becomes black or even welded together, it can be judged that the contact is ablated. This ablation will cause the contact resistance of the contact to increase sharply, resulting in the circuit being unable to conduct normally, and the equipment will not work properly. For example, in an automated food production line, if the AC contactor contact responsible for controlling the conveyor belt motor is burned, the conveyor belt will stop running and the entire production process will be forced to be interrupted, which will not only affect the production progress, but may also cause product quality problems.
Contact burnout is usually caused by a combination of factors. On the one hand, when the load current exceeds the rated load capacity of the contactor contact, it is like letting a small horse pull a large cart. The contact will heat up due to the excessive current and then burn out; on the other hand, when the contact pressure is insufficient, the contact area becomes smaller and the contact resistance increases, which will also generate too much heat and cause burnout; in addition, if there is an oxide layer or other impurities on the contact surface, it will also cause the contact resistance to be too high, and eventually cause contact burnout.
To prevent and solve the problem of contact burnout, daily maintenance is essential. You can regularly use sandpaper or a special contact cleaner to clean the oxide layer and dirt on the contact surface to ensure good contact. At the same time, check the pressure of the contact spring and adjust the compression of the spring to keep the contact pressure within the appropriate range. If the contact is severely ablated, it is necessary to replace the contact in time. Selecting high-temperature resistant and wear-resistant alloy contacts can effectively improve the service life and performance of the contact.
Coil overheating: a silent “invisible killer”
Coil overheating is another potential dangerous fault of AC contactors. It is like a silent “invisible killer” that damages the equipment unknowingly. When you touch the contactor, if you feel that the coil part is abnormally hot or even smell a burnt smell, it means that the coil is overheated. Coil overheating will not only accelerate the aging of the insulation layer and reduce its insulation performance, but in severe cases, it may also cause a fire, threatening the safety of the entire production environment. In some chemical companies, due to the flammable and explosive production environment, if the AC contactor coil overheats and causes a fire, the consequences are disastrous.
The causes of coil overheating are relatively complex. Voltage fluctuation is a common factor. When the actual working voltage is higher or lower than the rated voltage of the coil, the current in the coil will change, thus generating too much heat. A short circuit between coil turns will also cause the local current to increase, causing overheating. This is like a “short circuit channel” in the circuit, where the current passes through in a concentrated manner, generating a lot of heat. In addition, if the iron core is stuck during movement and cannot be normally attracted or released, the current in the coil will continue to be at a large value, which will cause the coil to overheat.
To avoid the harm caused by overheating of the coil, we can take a series of effective countermeasures. First, install a voltage stabilizer in the circuit to ensure that the voltage is stable within the appropriate range and provide a stable working voltage for the coil; secondly, regularly check the activity of the iron core, clean the oil and impurities on the surface of the iron core, and ensure that the iron core can move flexibly; if the coil is found to have been overheated and damaged, it is necessary to replace the coil of the same specification in time. When replacing, be sure to choose a reliable product to ensure that its performance meets the requirements.
Abnormal attraction: “strike signal” of the contractor
When the AC contactor has an abnormal attraction, it is like it has sent a “strike signal”, and the normal operation of the equipment will also be affected. Abnormal pull-in can manifest in various forms, such as contact jitter, just like people shivering in the cold winter. This jitter will cause the circuit to be on and off, affecting the stable operation of the equipment; there is also abnormal noise from the iron core, which is harsh and makes people know that there is a problem with the equipment at a glance; even more serious is that the contactor cannot be pulled in and the equipment cannot be started directly. In construction, the operation of large equipment such as tower cranes depends on the normal operation of AC contactors. If there is an abnormal pull-in, the tower crane cannot lift building materials normally, and the entire construction progress will be delayed.
Abnormal pull-in is usually caused by the following reasons. When there is oil on the surface of the iron core, it will affect the transmission of electromagnetic attraction, resulting in difficulty in pull-in; short-circuit ring breakage is also a common reason. The function of the short-circuit ring is to eliminate the vibration and noise of the iron core during the pull-in process. Once the short-circuit ring breaks, the iron core will produce strong vibration and noise, affecting the pull-in effect; in addition, spring failure will cause the spring’s elastic force to be insufficient or too large, unable to provide appropriate force, resulting in the contact failing to pull in or release normally.
For the problem of abnormal pull-in, we can take corresponding solutions. Clean the surface of the core regularly, use a clean cloth or detergent to remove oil stains, and ensure that the surface of the core is clean and tidy; if the short-circuit ring is found to be broken, replace the short-circuit ring of the same specification in time to ensure the normal operation of the core; for the spring problem, it is necessary to adjust the tension of the spring to restore it to the appropriate elastic force, and replace a new spring if necessary. Through these measures, the abnormal pull-in problem of the AC contractor can be effectively solved to ensure the normal operation of the equipment.
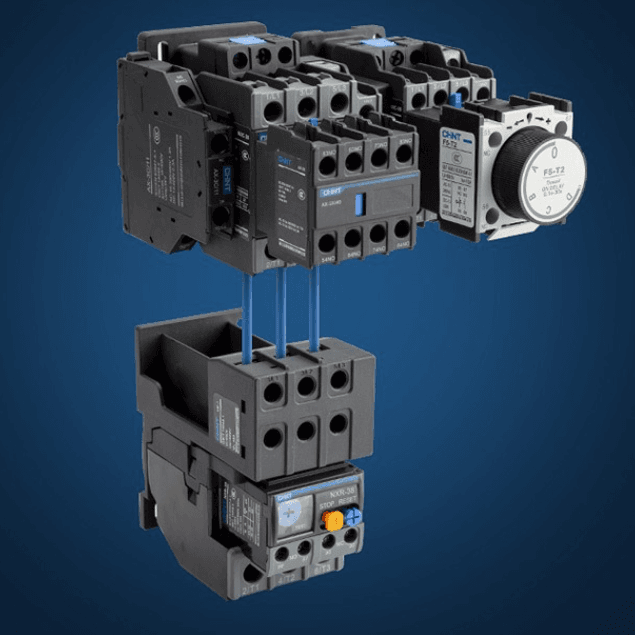
Selection and maintenance in different scenarios
Selection skills: Matching on demand is the hard truth
In the industrial field, the selection of AC contractors is like finding the most suitable shoes for different feet. Only accurate matching can ensure the efficient and stable operation of the equipment. Next, we will discuss the selection skills of AC contactors in detail for different application scenarios.
- Motor control: In the motor control scenario, since a large impact current will be generated when the motor starts, it is necessary to select an AC contactor with an arc extinguishing device to quickly extinguish the arc generated when the contact is disconnected to protect the contact and equipment. For example, in the motor control system of a large machine tool, an arc extinguishing device with excellent performance is required. At the same time, to ensure that the contractor can withstand the working current of the motor, its current capacity should be selected to be more than 1.5 times the rated current of the motor. For example, for a motor with a rated current of 20A, an AC contactor with a current capacity of at least 30A should be selected to ensure that the contactor will not be damaged due to excessive current during long-term operation.
- High dust environment: In dusty working environments such as coal mines and cement plants, dust can easily enter the interior of the AC contactor, contaminate the contacts, increase the contact resistance, and affect the normal operation of the contactor. Therefore, in this environment, sealed contactors should be used first. Sealed contactors have good dustproof performance, can effectively prevent dust from entering the interior, reduce the risk of contact contamination, and ensure the reliable operation of the contactor. For example, in the ventilation system of a coal mine, the use of sealed AC contactors can greatly reduce the failure rate caused by dust problems, ensure the stable operation of ventilation equipment, and provide a safe working environment for underground workers.
- Frequent operation scenarios: In automated production lines, cranes, and other equipment that require frequent operation, the frequent operation of AC contactors will cause their contacts and coils to be subjected to greater pressure, which is easy to causes component wear and damage. At this time, it is recommended to use DC-controlled AC contactors. When working, the coil current of the DC-controlled AC contactor is stable, and it will not generate an impact current like the AC coil, thereby reducing the impact and wear of the iron core and extending the service life of the contactor. For example, in the automated production line of automobile manufacturing, a large number of DC-controlled AC contactors are used to meet the needs of high speed and frequent start and stop of the production line, improve production efficiency, and reduce equipment maintenance costs.
Daily maintenance: the “golden rule” to extend life
The daily maintenance of AC contactors is like injecting a “maintenance secret recipe” into the equipment, which can effectively extend its service life and ensure that the equipment is always in the best operating state. The following are some “golden rules” for daily maintenance.
- Cleaning and maintenance: Regularly powering off and cleaning the AC contactor every month is an essential maintenance step. During the cleaning process, special attention should be paid to cleaning dust, oil, and other impurities on the contacts and iron core. These impurities will form an insulating layer on the surface of the contact and the core, affecting the electromagnetic attraction and contact performance, causing abnormal operation of the contactor. You can use a clean brush to gently brush off the dust, and then wipe the oil with a cloth dipped in an appropriate amount of detergent to ensure that the surface of the contact and the core are clean and tidy, providing good conditions for the normal operation of the contactor.
- Tightening inspection: It is very important to regularly check the tightness of the terminal. As the equipment runs, the terminal may become loose due to vibration and other reasons, which will increase the contact resistance, cause serious problems such as heating and even fire. Therefore, tools should be used to tighten the terminal regularly to ensure a firm connection. During each equipment overhaul, the tightness inspection of the terminal should be taken as a key project to promptly detect and solve the looseness problem and ensure the reliability of the circuit connection.
- Functional test: Using a multimeter to perform functional testing on the AC contactor is an effective means to detect potential hidden dangers. The coil resistance can be tested regularly. Under normal circumstances, the coil resistance should be within the specified range. If the resistance value is too large or too small, it may mean that the coil is faulty and needs further inspection and treatment. At the same time, it is also critical to detect the on-off state of the contacts. Through the measurement of the multimeter, it can be determined whether the contacts can be closed and opened normally. Once the contact is found to be abnormal, the cause should be found out in time and repaired or replaced to avoid the expansion of the fault and affect the normal operation of the equipment.
Pitfall avoidance guide: Have you fallen for these misunderstandings?
- Myth 1: The larger the contractor, the better
When choosing an ACcontractorr, many people tend to fall into the misunderstanding of “the larger the better”, believing that a larger contactor can provide stronger performance guarantees. But the actual situation is not that simple. In a small food processing workshop, the load current of the equipment is relatively small. If an oversized AC contactor is selected, it will not only greatly increase the procurement cost but also cause a waste of space. Because large contractors are large in size, installation and layout will become difficult for small equipment with limited space. Moreover, when an oversized contactor is working, the action characteristics of its electromagnetic system and contact system may not match the actual load, which will reduce work efficiency and increase energy consumption. The correct approach is to calculate the required contractor specifications accurately based on the actual load current and frequency of use. For example, for a device with a rated current of 10A, it is sufficient to select a contractor with a rated current of about 12-15A, which can not only meet the normal operation requirements of the equipment but also avoid unnecessary cost waste and performance loss. - Myth 2: The Arc extinguishing device is dispensable
The arc extinguishing device plays a vital role in AC contactors, but some users think it is dispensable, which is an extremely dangerous misunderstanding. When the contacts of the AC contactor disconnect the circuit, a high-temperature arc will be generated between the contacts due to the rapid change of current. If there is no arc extinguishing device, these arcs will continue to exist, which will not only burn the contacts and shorten the service life of the contacts but may also cause serious safety accidents, such as fire. In some flammable and explosive chemical production environments, once the arc triggers the combustion or explosion of flammable and explosive materials around, the consequences will be disastrous. The arc extinguishing device can quickly lengthen and cool the arc through special designs, such as magnetic blowing type and grid type, so that it can be extinguished quickly, thereby protecting the safety of the contacts and equipment. Therefore, the arc extinguishing device is by no means a dispensable accessory but a key component to ensure the safe operation of the AC contactor, and its role cannot be ignored under any circumstances.
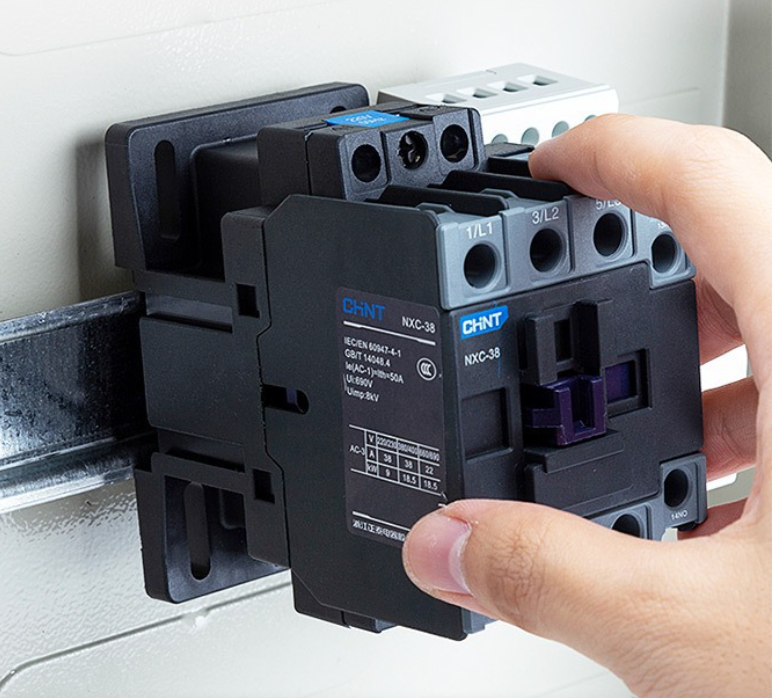
Advantages of smart contactors
- Real-time monitoring: Smart contractors are equipped with advanced sensors, which are like sensitive “sensory organs” installed for equipment, and can monitor key operating data such as current and temperature in real time. These sensors feed back the collected data to the control system in real time to achieve all-around monitoring of the equipment’s operating status. Once abnormal data is found, such as a sudden increase in current or temperature exceeding the normal range, the system will immediately issue a fault warning to remind the staff to deal with it in time. In the power distribution system of the smart grid, the smart contactor monitors the current and temperature in real time. When it is found that a certain line is overloaded, it will quickly issue a warning signal, and the staff can adjust the power distribution in time to avoid line failures caused by overloading and ensure the safe and stable operation of the power grid.
- Energy saving and consumption reduction: The use of low-power coil design is a key measure for smart contactors to achieve energy saving and consumption reduction. The coil of the traditional contactor consumes a lot of electricity when it is powered on for a long time, while the smart contactor greatly reduces the power consumption of the coil by optimizing the coil structure and control method. This not only reduces energy waste and reduces the electricity cost of enterprises but also helps to achieve the goal of energy saving and emission reduction and contributes to environmental protection. Taking a large factory as an example, after replacing traditional contactors with smart contactors, a large amount of electricity can be saved every year, production costs can be reduced, and carbon emissions can be reduced, achieving good economic and environmental benefits.
- Remote control: Supporting IoT access is another significant advantage of smart contractors. Through IoT technology, smart contractors can be easily connected to smart terminals such as mobile phone APPs to achieve remote switch control. No matter where you are, as long as there is network coverage, you can operate the smart contactor through the mobile phone APP, just like holding the control button in your hand. In the smart home system, users can remotely control the smart contactor through the mobile phone APP to achieve remote switching of home electrical appliances, such as turning on the air conditioner and water heater in advance on the way home from work, which brings great convenience to life.
Mastering the operation and maintenance logic of AC contactors can not only quickly troubleshoot faults but also extend the life of equipment and reduce operation and maintenance costs through scientific selection and maintenance. For electricians and industrial practitioners, this is not only a “must-have skill” to ensure production but also an important entry point for embracing industrial intelligence.